Earlier this year, I built a 7′ rocket to obtain L1 and L2 certifications from the National Rocketry Association. I flew it twice to earn my certifications, and since then I have flown it four more times to test various other systems including a reefed parachute and circumferential disreefing mechanism, a custom flight control board, and a payload interface system. It remains in good condition and ready to launch.
I built the rocket from scratch and developed a new system to mount the fins and the motor tube. Removable ¼” plywood fins are clamped between two ½” plywood centering rings. Three steel ¼”-20 threaded rods with jam nuts provide the clamping force. A 38 mm fiberglass motor tube is epoxied to a ½” plywood thrust plate and a ½” plywood centering boss. All plywood is laser-cut.
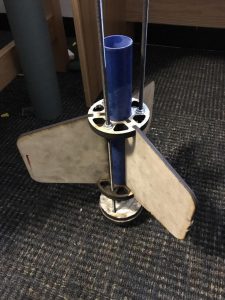
After the fins are installed, the motor tube is pushed up through the centering rings and the thrust plate is secured with nuts onto the threaded rods. The threaded rods do not take the load from the motor; they only serve to keep the thrust plate from falling out the back of the rocket during descent. The thrust is transferred directly from the motor tube to the thrust plate to the bottom of the body tube.
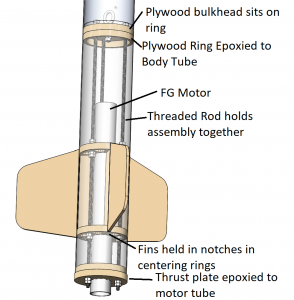
The vehicle is equipped with redundant flight computers and separation charges. It has two parachute/payload bays and is capable of carrying a 15″ payload of over 2.5 kg (although a large payload requires that the fins be replaced, which is why they are removable). In total, the rocket is 83″ long and has a stability margin of 2.2 calibers without a payload.
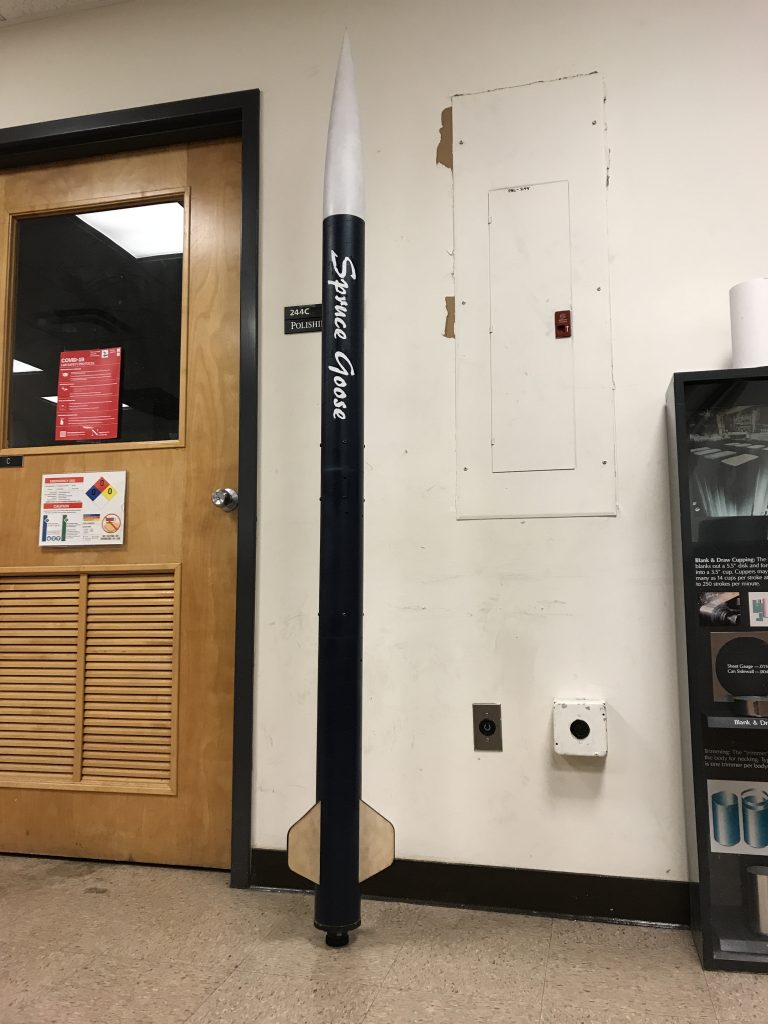